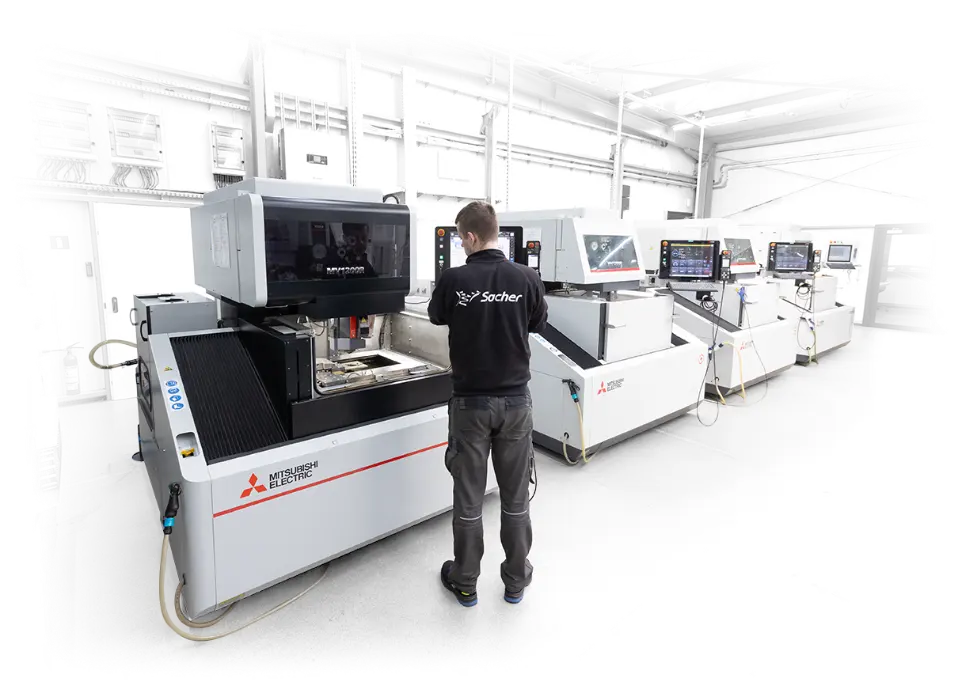
What exactly does the wire EDM process involve?
Wire EDM uses wire-shaped electrodes that cut material through electric discharges. This allows for precise cutting of materials with complex contours (e.g., curved profiles) while maintaining high accuracy.
Is EDM effective only for producing new parts?
No, the application of EDM also includes tool refurbishment and repair of damaged molds, which extends their lifespan and reduces costs.
What materials can be machined using EDM?
EDM is mainly used for difficult-to-machine materials such as tool steel, cemented carbides, and titanium alloys. The process requires low mechanical forces, making it suitable for parts sensitive to deformation.
Does sinker EDM differ from wire EDM in terms of precision?
Both methods offer high precision; however, sinker EDM is typically used for creating pockets and grooves in parts (e.g., injection molds), while wire EDM allows for cutting external contours with very complex geometry.