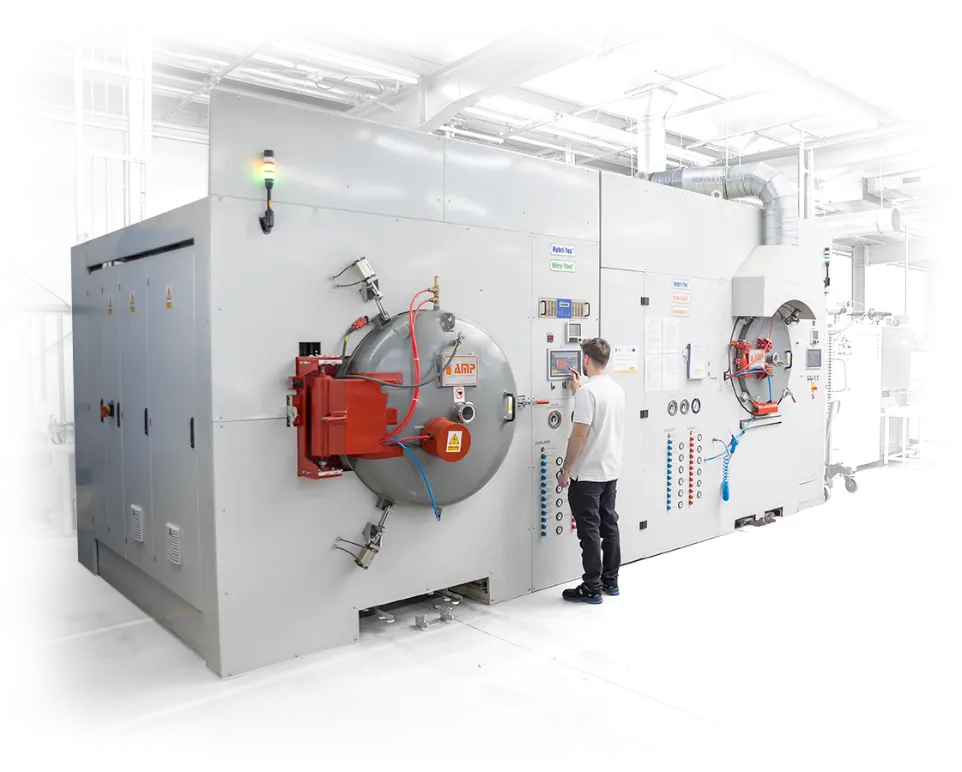
Czy obróbka termiczna wpływa na cały przekrój detalu?
Zależy to od rodzaju procesu. W klasycznym hartowaniu i odpuszczaniu zmiany strukturalne obejmują cały przekrój (przy odpowiednim czasie i temperaturze wygrzewania). Natomiast takie zabiegi jak nawęglanie czy azotowanie wpływają głównie na warstwę wierzchnią, pozostawiając rdzeń w innym stanie.
Co zrobić, aby uzyskać wysoką wytrzymałość bez utraty plastyczności?
Zazwyczaj stosuje się hartowanie i odpuszczanie w starannie dobranym zakresie temperatur, co pozwala uzyskać równowagę pomiędzy twardością (wytrzymałością) a plastycznością. Kluczowe jest dobranie odpowiedniego gatunku stali (zawartości węgla i pierwiastków stopowych), a następnie przeprowadzenie kontrolowanego wygrzewania i chłodzenia, tak aby struktura nie była zbyt krucha przy jednoczesnym zachowaniu wysokiej wytrzymałości.
Jak ograniczyć pęknięcia w trakcie hartowania?
Aby ograniczyć ryzyko pęknięć poprzez dobór mniej agresywnego środka chłodzącego (np. olej zamiast wody), zapewnienie równomiernego nagrzewania i chłodzenia detalu (np. w piecach o kontrolowanej atmosferze), stosowanie wstępnego podgrzewania w razie dużych różnic temperatur oraz unikanie ostrych zmian przekrojów i naprężeń w strukturze detalu.
Dlaczego szybkość chłodzenia jest tak ważna?
Szybkość chłodzenia jest kluczowa, ponieważ wpływa na rodzaj powstającej mikrostruktury i finalne właściwości materiału. Zbyt wolne chłodzenie może nie umożliwić przemiany w twarde fazy (np. martenzyt), natomiast nadmiernie gwałtowne chłodzenie może powodować duże naprężenia i prowadzić do pęknięć. Dlatego często stosuje się odpowiednio dobrane media chłodzące, na przykład olej hartowniczy, który zapewnia bardziej kontrolowane tempo chłodzenia i mniejsze ryzyko uszkodzeń.
Jak obróbka cieplna wpływa na finalny produkt?
Obróbka cieplna pozwala nadać materiałowi wymagane właściwości mechaniczne (twardość, wytrzymałość, odporność na zużycie) i zoptymalizować jego mikrostrukturę. Wpływa to bezpośrednio na jakość, trwałość oraz funkcjonalność finalnego produktu, umożliwiając wytwarzanie bardziej wytrzymałych elementów o ściśle kontrolowanych parametrach.
Jaka jest przewaga azotowania plazmowego
Azotowanie plazmowe (jonowe) pozwala na precyzyjną kontrolę warunków procesu, w tym temperatury i składu atmosfery. Zapewnia bardziej jednolitą warstwę azotowaną o wysokiej twardości i odporności na zużycie. Charakteryzuje się mniejszymi odkształceniami elementu w porównaniu z klasycznym azotowaniem gazowym. Proces jest też zwykle czystszy, dzięki zredukowanej ilości wytwarzanych zanieczyszczeń, a dodatkowo możliwa jest obróbka detali o złożonych kształtach.
Jaka jest przewaga procesów próżniowych?
Procesy próżniowe zapewniają minimalne utlenianie oraz decarburyzację powierzchni, co przekłada się na wysoką czystość i stabilność wymiarową obrabianych elementów. Dodatkowo umożliwiają bardzo precyzyjną kontrolę parametrów (temperatury, ciśnienia, składu gazów), prowadząc do uzyskania powtarzalnych rezultatów oraz lepszej jakości finalnego wyrobu.