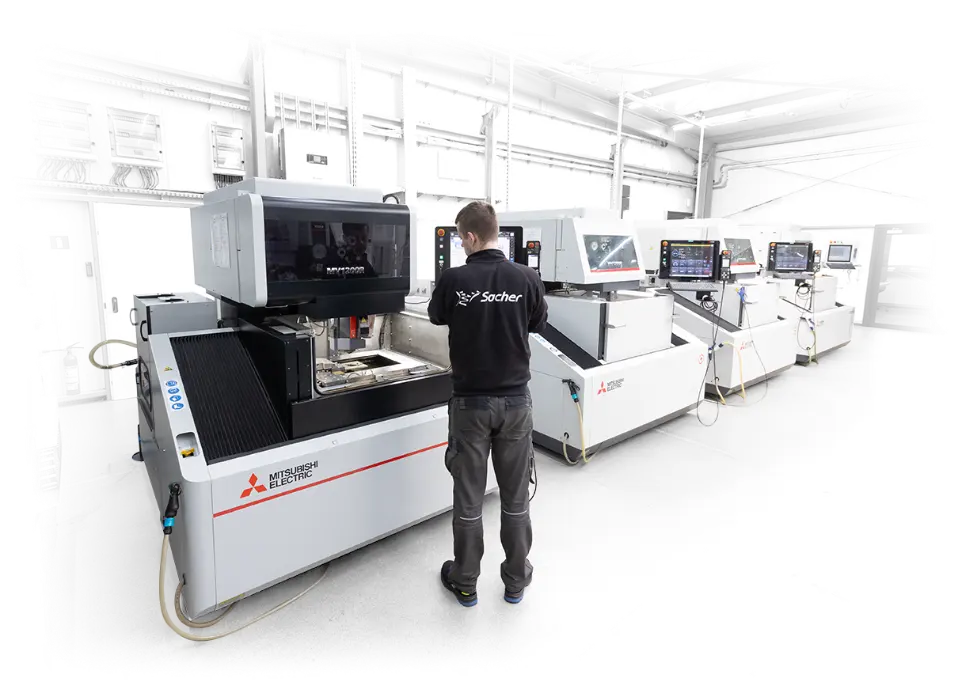
Na czym dokładnie polega proces elektrodrążenia drutowego?
Elektrodrążenie drutowe wykorzystuje elektrody w formie drutu, który tnie materiał przy pomocy wyładowań elektrycznych. Dzięki temu cięcie materiałów o skomplikowanych zarysach (np. profile łukowe) jest możliwe z zachowaniem wysokiej precyzji.
Czy elektrodrążenie sprawdza się tylko w produkcji nowych elementów?
Nie, możliwość zastosowania elektrodrążenia obejmuje także regeneracji narzędzi i naprawę uszkodzonych form, co pozwala na wydłużenie ich żywotności oraz redukcję kosztów.
Jakie materiały można obrabiać metodą elektrodrążenia?
Elektrodrążenie stosuje się głównie do materiałów trudnoskrawalnych, takich jak stal narzędziowa, węgliki spiekaneczy stopy tytanu. Proces nie wymaga dużych sił mechanicznych, więc nadaje się do elementów wrażliwych na odkształcenia.
Czy elektrodrążenie wgłębne różni się od obróbki drutowej pod względem precyzji?
Obie metody zapewniają wysoką precyzję, jednak elektrodrążenie wgłębne jest zwykle wykorzystywane do tworzenia kieszeni i żłobień w detalu (np. formy wtryskowe), podczas gdy drutowe pozwala na wycinanie konturów zewnętrznych o bardzo złożonej geometrii.